Contamination is defined as any substance which is foreign to a lubrication system and damaging its performance. Even when no immediate failures occur, high contaminations levels can accelerate component wear and in turn, contribute to inefficient system operation, seizure of parts, higher temperature or vibration levels, leakage and loss of control. All of these phenomena are the result of direct mechanical action between the contaminants and system components. Contamination can exist as gas, liquid or solid.
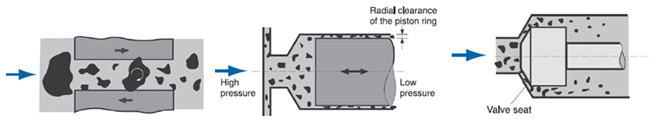
Contaminations come from two basic sources: they either enter the system from outside (ingestion) or are generated from within (ingression). Most systems ingest contaminants through such components as inefficient air breathers.
|